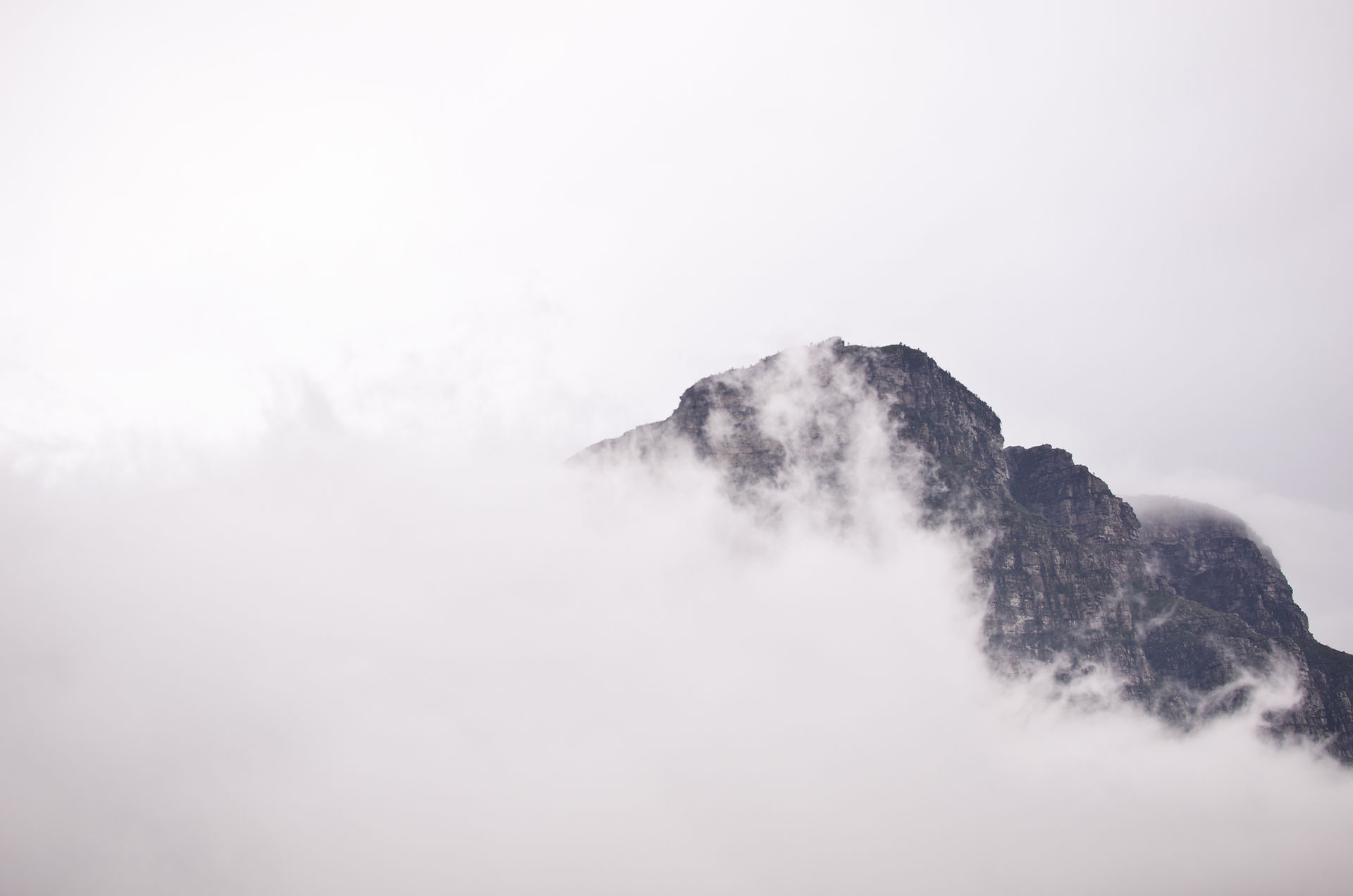

Prototype III after SolidWorks Rendoring
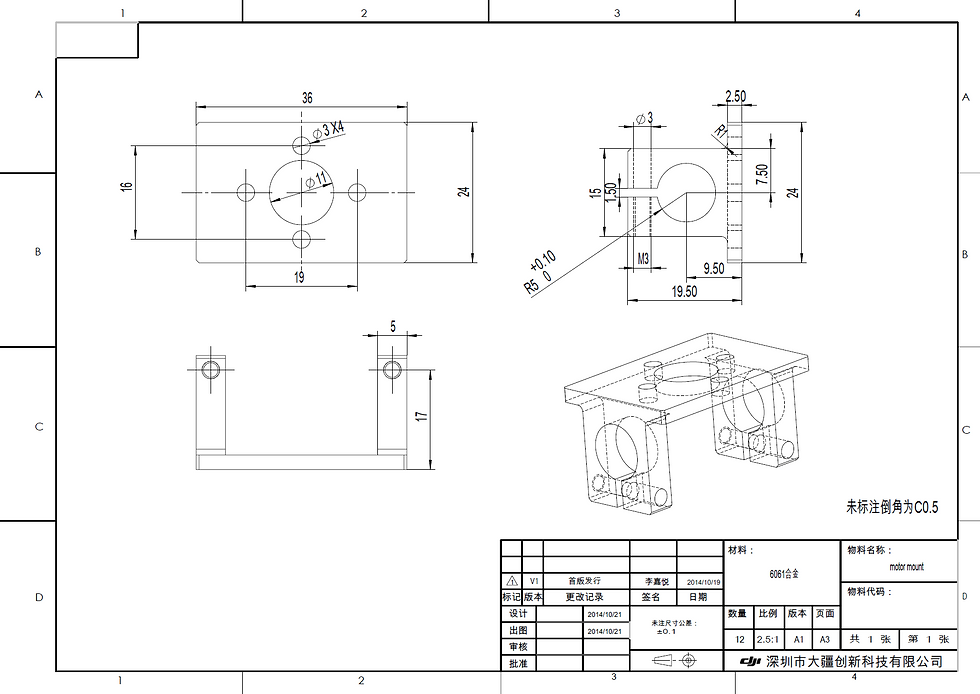
Engineering drawing for a Servo Mount for manufacturing

Lift Force with an angle of attack of 3 degrees -- Prototype III

Prototype III after SolidWorks Rendoring
Developed a UAV that achievece quadcopter flight and fixed-wing flight simutaneously
Prof. Moses NG's Lab, HKUST
Team Leader
2014.6 -- 2015.5
-
Implemented a tiltrotor mechanism that granted a fixed-wing aircraft with Vertical Take-Off and Landing ability, yet maintained a 60% more energy efficiency compared with a DJI Phantom 3.
-
Prototyped the UAV for 3 generations with 3D CAD in CATIA and optimization based on FEA and test flight results.
-
Designed for aerodynamic efficiency and stability in XFOIL, and corresponding selections for air foils, propellers and motors.
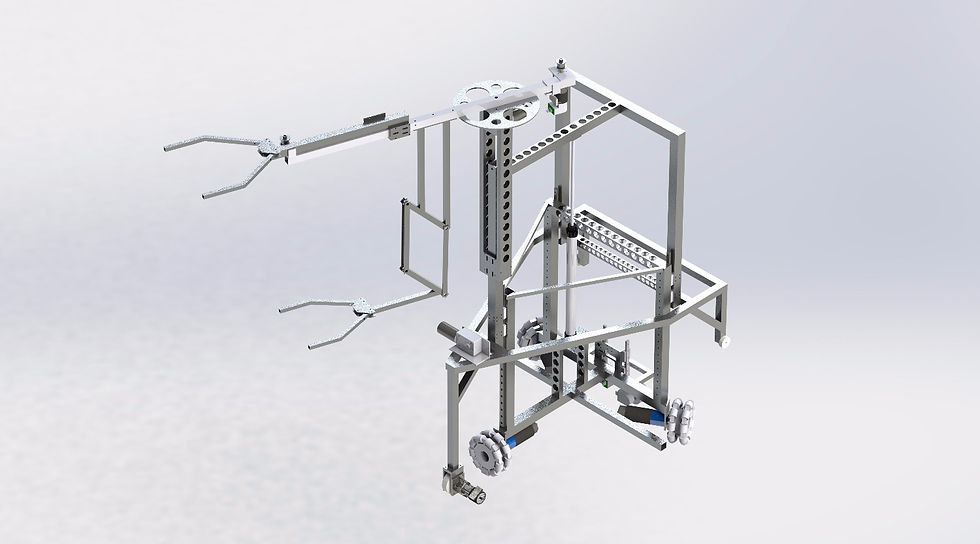
3rd Generation of the Collector Robot in after 3D Rendering
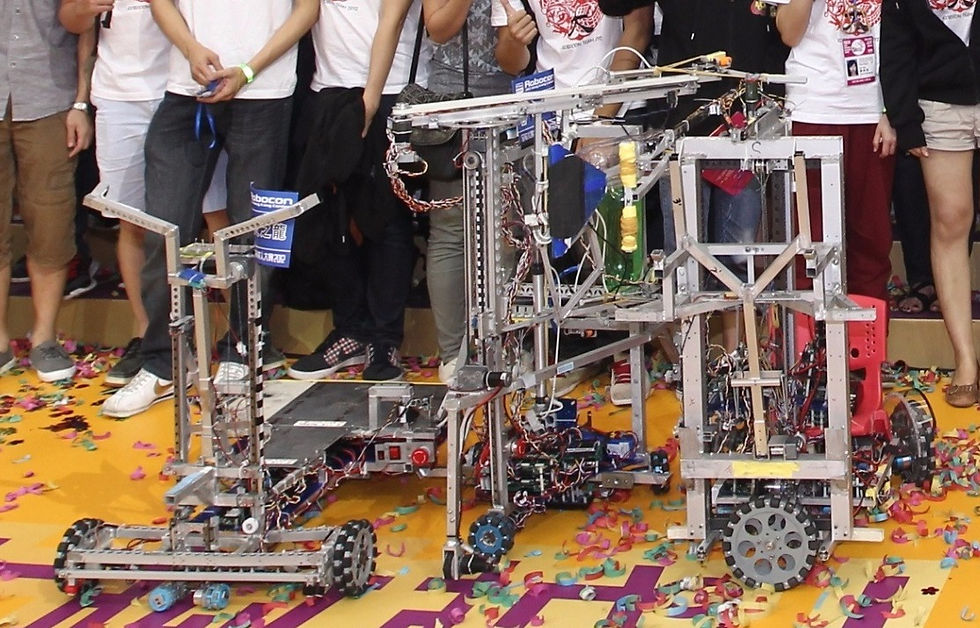
2 automatic and a manual Robots are made for the Contest. Each one of them is optimized through 3 generations.
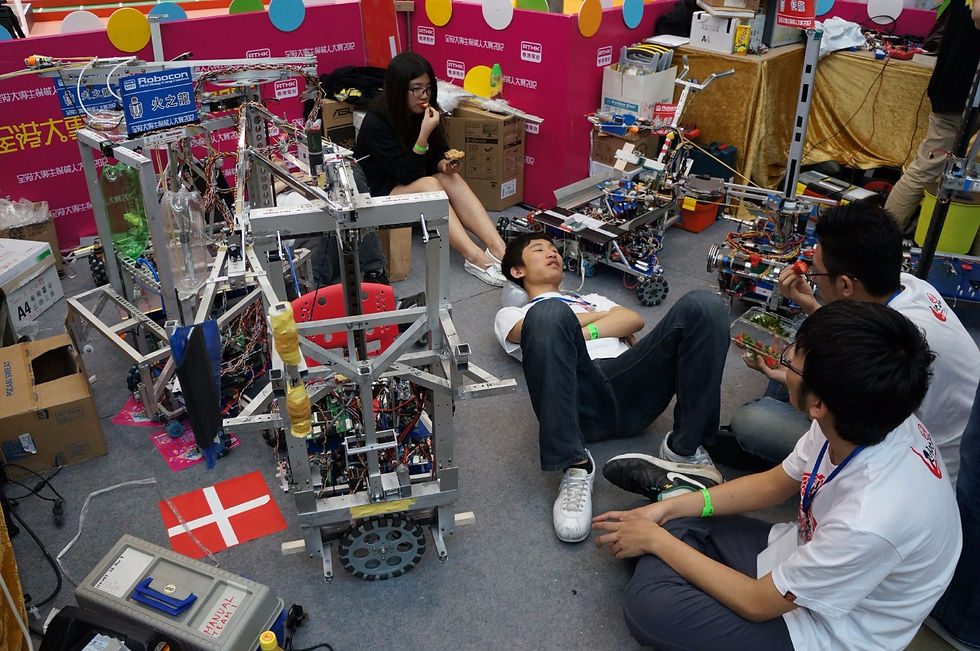
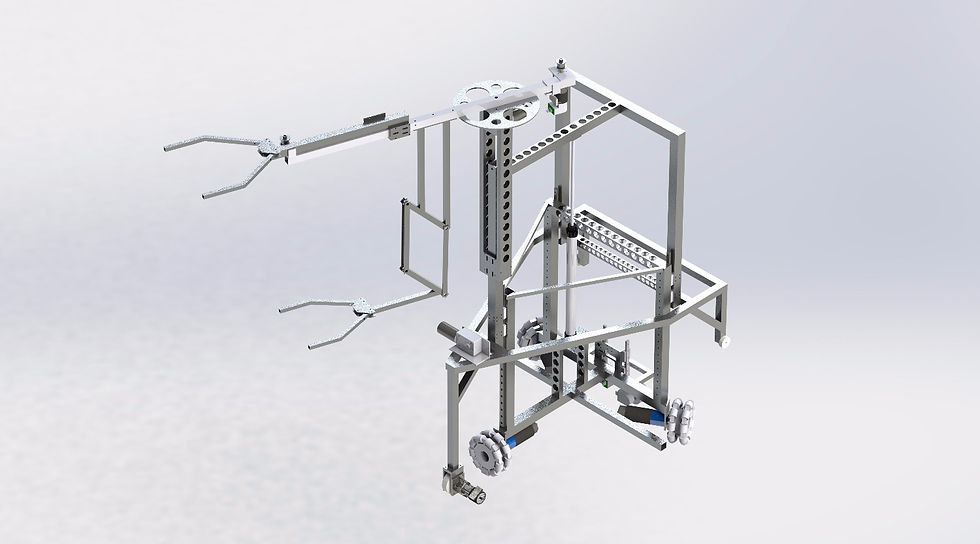
3rd Generation of the Collector Robot in after 3D Rendering
Prototyping an automatic robot capable of climbing stairs, collecting and placing objects
HKUST Robotics Team -- Robocon Team
Mechanical Engineer
2011.9 -- 2012.6
-
Prototyped a pneumatic/servo driven robot with robotic arms for 3 generations with 3D CAD in SolidWorks.
-
Created engineering drawings with GD&T, manufactured the robots in machine shop and conducted test runs.
-
Broke the robot contest record in Hong Kong by accomplishing the 3-minute limit task in 75 seconds.
-
Knowledge in the use of electrical devices (i.e. various sensors, switches, air control valves, servo motors, DC motors and drivers and etc.)

Von Mises Stress in the connecting rod under maximum bending moment
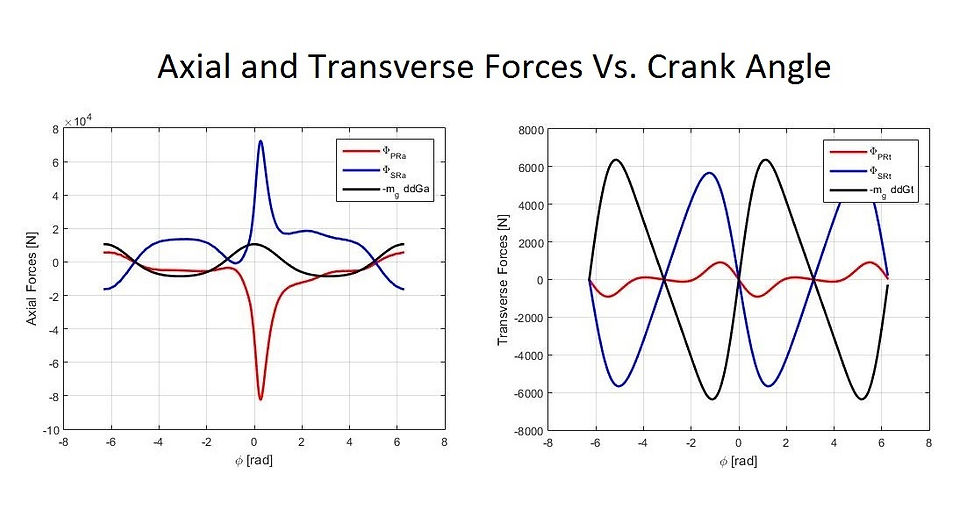
Load Analysis in MATLAB based engine data
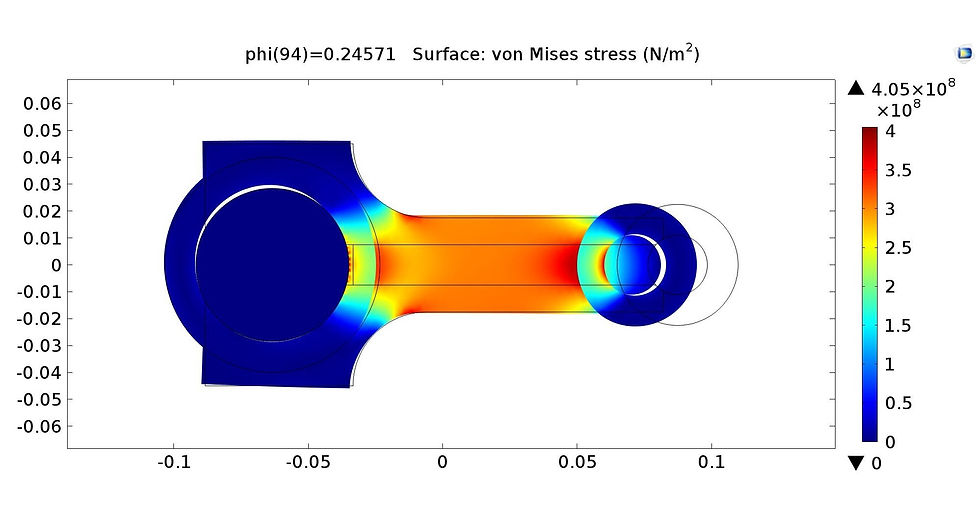
Von Mises Stress in the connecting rod under maximum axial force (compression in this scenario)

Von Mises Stress in the connecting rod under maximum bending moment
Conceptual Design of a Connecting Rod for Ford Mustang GT
Course project for MAE 196A Failure Design
-
3D CAD in CATIA V5
-
Load analysis in MATLAB from engine data
-
2D FEA and optimization in COMSOL
-
3D FEA and optimization in Abaqus
-
Design for fatigue in MATLAB based on rainflow-counting algorithm, yielded with a reliability of 99.99%.

Micro bridge are manufactured, to determine the residual stress in the wafer based on the buckling result

SU-8 pattern for micro channels after hard Bake

Droplets with various sizes are achieved by controlling the flow rate in the Micro Fluid Channel

Micro bridge are manufactured, to determine the residual stress in the wafer based on the buckling result
Clean Room and Micro Manufacturing Experience
Course MAE 196A Nano and Micro Manufacturing
-
Photolithography and Wet Etching
-
Soft Lithography and Oxygen Plasma Boding
-
Micro and Nano Imprinting

The main frame of the wind turbine -- with the main shaft connected

Bolt connection between the main frame and the subsidiary frame
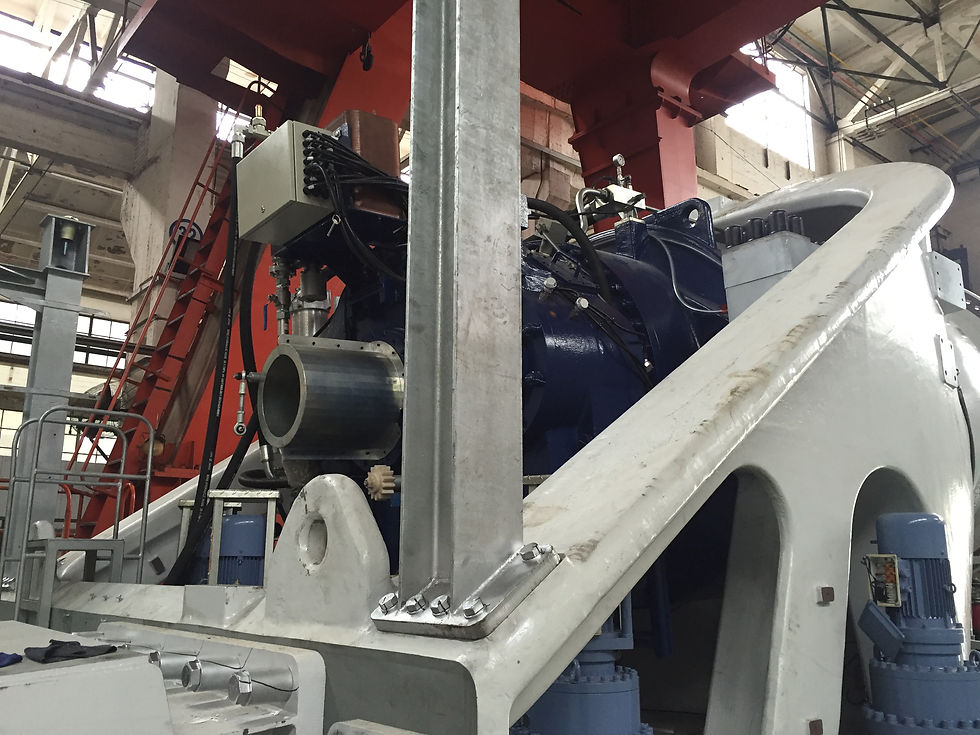
Bolt connection between the main frame the electronic device holder

The main frame of the wind turbine -- with the main shaft connected
Design of a 2 MW Wind Turbine for Application in Vietnam
Beijing JINGCHENG New Energy Co., Ltd.
Mechanical Design Engineer Intern
2016.6 -- 2016.9
-
Developed 3D CAD models for the cast iron main frame of the wind turbine using SolidWorks, and produced engineering drawings specifying GD&T for manufacturing.
-
Stress analysis in Abaqus and corresponding optimization for the main frame and its bolting connection under various loading condition obtained in GH Bladed.
-
Integrated the hoisting component with the casting and avoided using expensive commercial product.
-
Fatigue analysis of the main frame under rated loading in nCode based on rainflow-counting algorithm
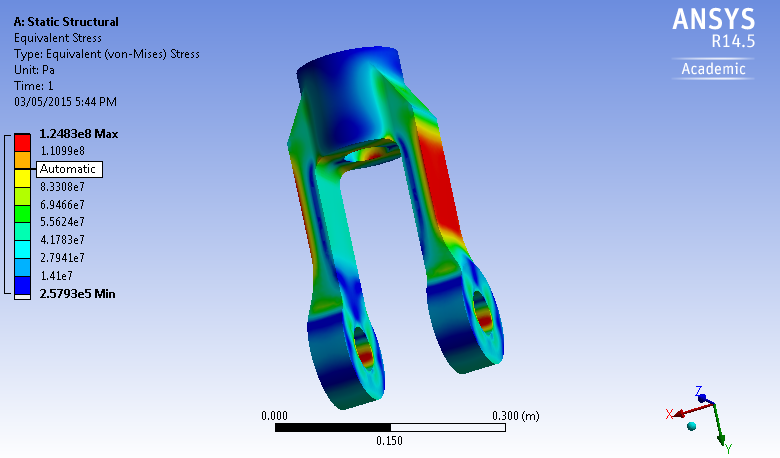
The equivalent stress principle is used for this static loading design
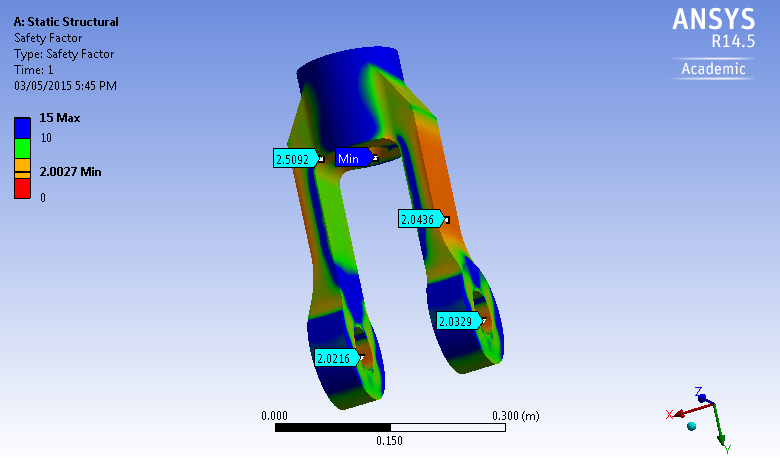
The Component is designed with a safety factor of 2. Points for potential failure are highlighted
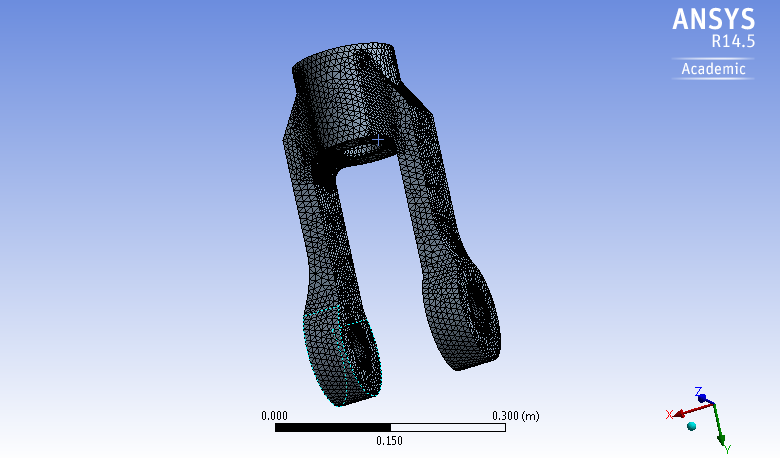
The Component is finely meshed with even finer mesh at potential failure zones
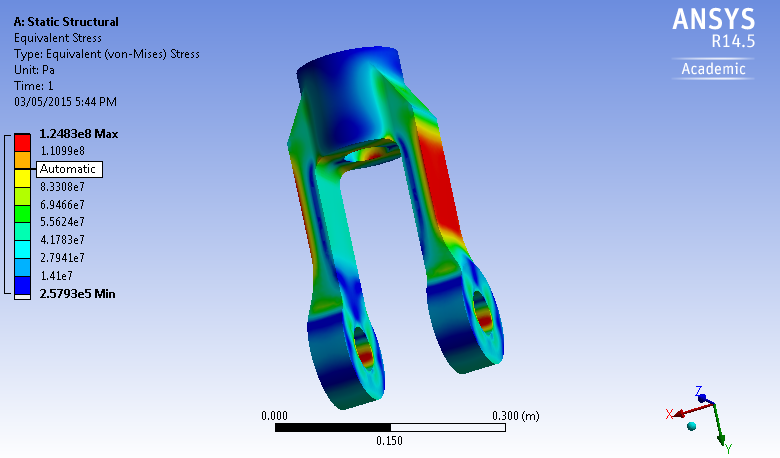
The equivalent stress principle is used for this static loading design
Conceptual Design of a Connecting Component
Course project for MECH 4450 FEA
-
3D FEA in ANSYS and SolidWorks
-
Design optimization and weight reduction
-
Converging study in ANSYS